What’s below your feet? Foundation talk about… foundation types.
As you might imagine, at Shield Foundation Repair, we see A LOT of foundations because, well, it’s what we do. Each has its own advantages and disadvantages, and each requires specific repair techniques. Years of experience and thousands of repairs on a wide range of foundation types have gone into our knowledge base.
The foundations we deal with are of four general types:
INSULATED CONCRETE FORM (ICF) FOUNDATIONS
What is an ICF foundation?
ICF Forms are two rigid polyurethane or polystyrene foam sheets separated with plastic separators. These separators determine the wall thickness and hold the mold in place for rebar reinforcement. Generally used in new home building, however form-work problems can occur, leading to leaking issues. At Shield Foundation Repair, we have seen many problems with ICF Form basements.
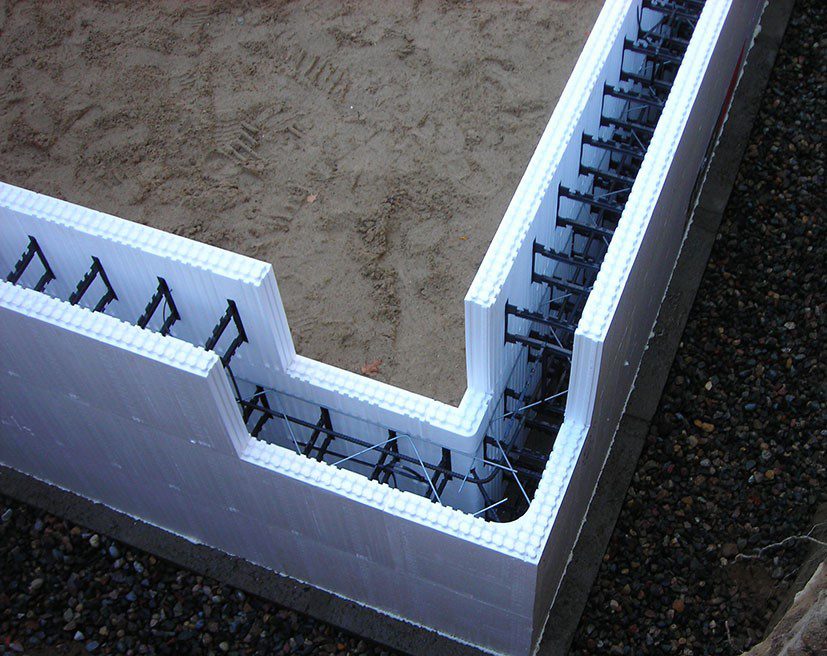
Disadvantages of ICF foundation construction:
- ICF foundations usually cost more to complete versus the standard wood form and pour.
- ICFs require extra support during setup to ensure the forms remain in place before and after concrete pours.
- More care is required to select the correct concrete slump and the aggregate size to ensure it meets the manufacturer’s specifications.
- Requires a membrane on the outside because the snap ties may have a wick effect.
- The thermal advantage may be questionable since both sides of the foundation are insulated. In addition, studies show higher energy efficiency during colder months but less during the warmer months.
- Snap ties used to secure the form also mean more penetrations through the concrete, resulting in more opportunities for water to penetrate, resulting in degradation of the overall concrete wall in time.
- Diagnosing ICF foundation issues is more difficult and requires significant expertise with this type of foundation application.
Workmanship Problems
- Not properly supporting the forms when the concrete is poured, often from being in a rush or to save costs. Crews may not properly vibrate or tamp the concrete when pouring to prevent blowouts in the form leaving areas of the foundation with honeycombed voids. Specifically, this is the problem we see most frequently.
- Wood forms around the openings installed without leaving the bottom sill plate open for concrete to be pumped into can leave large voids in these areas, which are often remedied by filling with foam that can degrade over time.
- Builders may use the wrong recommended aggregate size and slump by the manufacturer.
PRESSURE TREATED WOOD FOUNDATIONS (PWF)
What is a wood foundation?
Though its name might lead you to believe that the entire foundation is of wood, in fact only the below-grade foundation walls of a PWF are wood. The base is typically a concrete slab atop a bed of crushed rock or gravel. The wood used in PWFs is pressure treated, providing resistance to mold, fungus, and rot.
A wood foundation must withstand lateral pressures from the surrounding soil as well as environmental loads like wind, rain, and snow, which add pressure onto the foundation.
While treated lumber is resistant to moisture, it is still necessary to waterproof the foundation; use film, fluid applied sealants, caulking, and other materials to create a moisture-proof seal; and assure proper drainage.
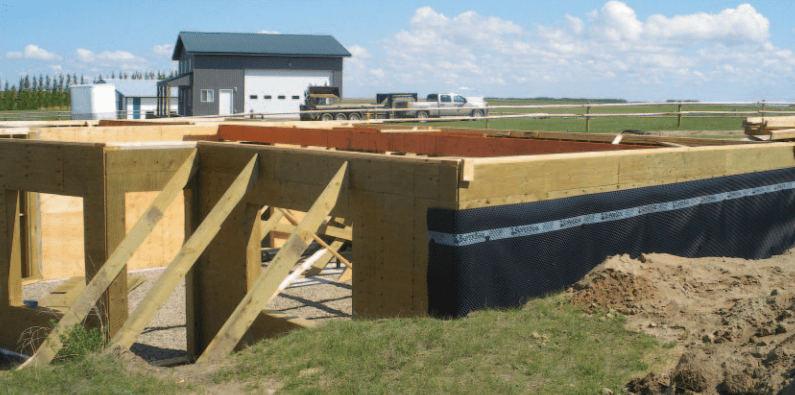
Disadvantages of wood foundations
- Damage from rot and insects. If a wood foundation is properly built and the site is well-drained, a PWF can last for decades. However, if moisture seeps in or the insect resistance of treated wood fails, replacing portions of a wood foundation may be costly.
- Expense. Wood foundations are more expensive to build than those from concrete.
- Novelty of PWFs. While countless homes have been built with PWFs, concrete foundations, whether poured or made of blocks, remain the norm. Due to this fact, getting a PWF home insured may be problematical.
- Toxicity of materials. The chemicals used to pressure treat the wood used in PWFs may cause homeowners to consider health and environmental dangers and affect home selling price as a result.
CINDER BLOCK FOUNDATIONS
What is it?
Cinder block foundations often use large, hollow concrete blocks. However, sizes can vary depending on the building’s weight load. To optimize strength and stability, workers install the blocks in a running bond pattern and may insert steel reinforcing bars in the core of the blocks. Mortar secures the blocks together, which rest on concrete footings.
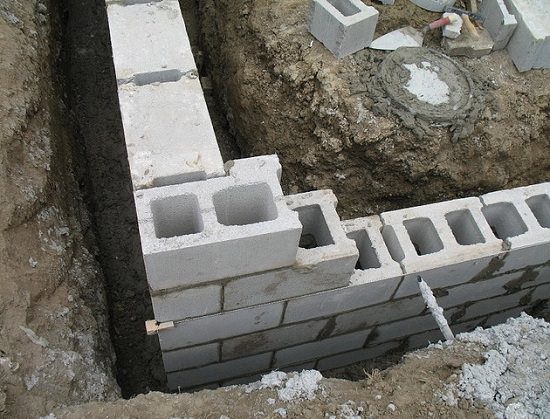
Disadvantages of cinder block foundations
- Cinder block units are heavy to manage.
- A cinder block wall often requires installation of an air and moisture barrier, which adds another trade and more labour.
- Improperly reinforced cinder blocks produce weak foundations.
- Water and weather wear down the mortar used to join the blocks together – this can cause leaks.
- Cinder block foundations may bow and buckle if the water in the soil around a structure builds up, resulting in costly repairs.
- Cinder block foundations have good load-bearing strength; however, the foundation will lose its lateral strength if not grouted and reinforced with rebar.
POURED CONCRETE FOUNDATIONS
What is a poured concrete foundation?
Poured concrete foundations involve constructing and properly securing large, heavy, wooden walls (forms). Next, in one continuous pour, workers pour concrete into the forms to cure on site. Rebar, installed in the footing, limits weak points and joints.
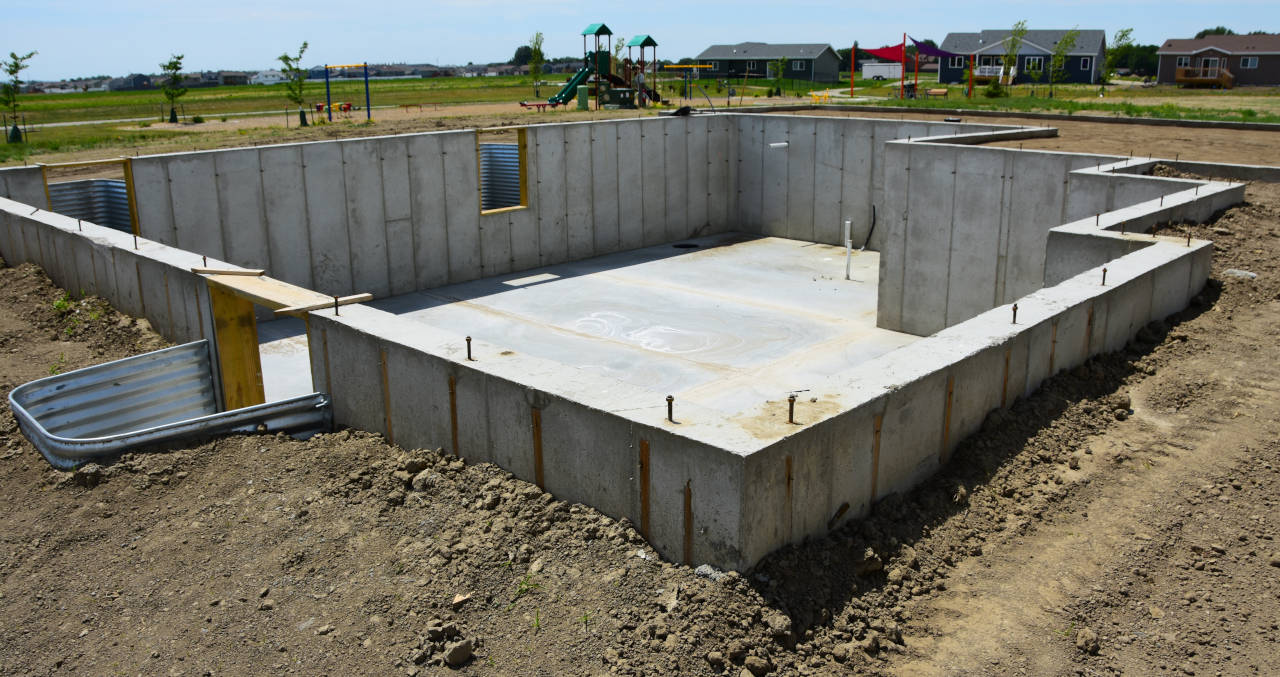
What are the disadvantages?
- If spalling (when the concrete surface peels, crumbles, or flakes off) occurs during curing, the poured concrete foundation can lose its strength.
- Poured concrete foundations cost more than cinder block foundations.
- Contractors may find it difficult, time-consuming, and costly to truck in wet concrete to the job site, adding to the build cost.
- Water leakage issues are common in older concrete foundations.
- Poured concrete can crack and leak again if the root cause is improperly identified and an inadequate repair completed.
- Poured concrete walls may leak moisture through non-structural cracks in the wall (where the wall and floor meet, at the top of the foundation wall or through the porous concrete).
- Leaks can happen if the foundation drops, settles, or sinks due to the soil below the foundation collapsing.
- Dry spots in the concrete wall may occur by improper grading.
- Poured concrete foundations usually have low R-values less than 3.
There’s more than one way to build a foundation. At Shield Foundation Repair, we have seen them all. We pride ourselves on being able to provide the right solution for almost any foundation we come across. Whatever foundation type you have, we can make it right. Call us today at 780 760 4900 to talk about the options available.